Ever wondered about the secret sauce behind those durable tungsten carbide burrs you adore? Well, buckle up, because I’m about to take you on a riveting journey behind the scenes at ShenTools! Let’s delve into the art and science of producing these little marvels.
Tungsten carbide burrs are made by blending tungsten carbide, a hard compound, with a metal binder, usually cobalt. The mixture undergoes a powder metallurgy process that includes pressing and sintering. The result is a dense, durable material that is then meticulously shaped into burrs.
So, why should you care? Because knowing the intricacies of the process will make you appreciate the precision and dedication that goes into every burr you hold in your hand. And let me tell you, here at ShenTools, we’re all about precision and dedication.
What’s the First Step in the Process?
Tungsten carbide production starts with tungsten ore extraction from mines. This ore undergoes a series of refining processes to produce pure tungsten powder. Simultaneously, carbon is added to form a fine tungsten carbide powder. This is our base ingredient, and quality control starts right here!
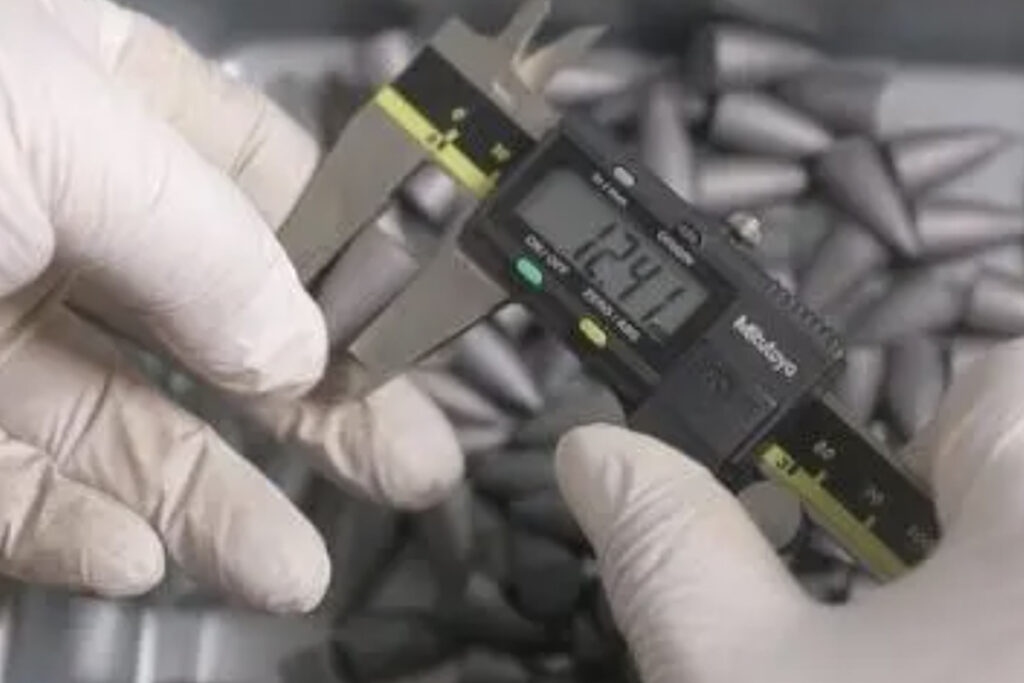
And the Binder?
A binder, usually cobalt, is then mixed with the tungsten carbide powder. This blend ensures that our burrs are not just hard but also tough. Think of it as the secret handshake of the metallurgy world – it’s what gives our burrs their superstar status in durability.
Pressing and Sintering: What’s That About?
After blending, the powder mixture is compacted into a desired burr shape using a high-pressure press. Think of it as a burr’s first step into the world. After pressing, it’s on to sintering. This involves heating the compacted shape in a furnace under a controlled atmosphere, bonding the particles together and increasing the material’s density. It’s like sending the burr to a spa day – emerging rejuvenated and more robust!
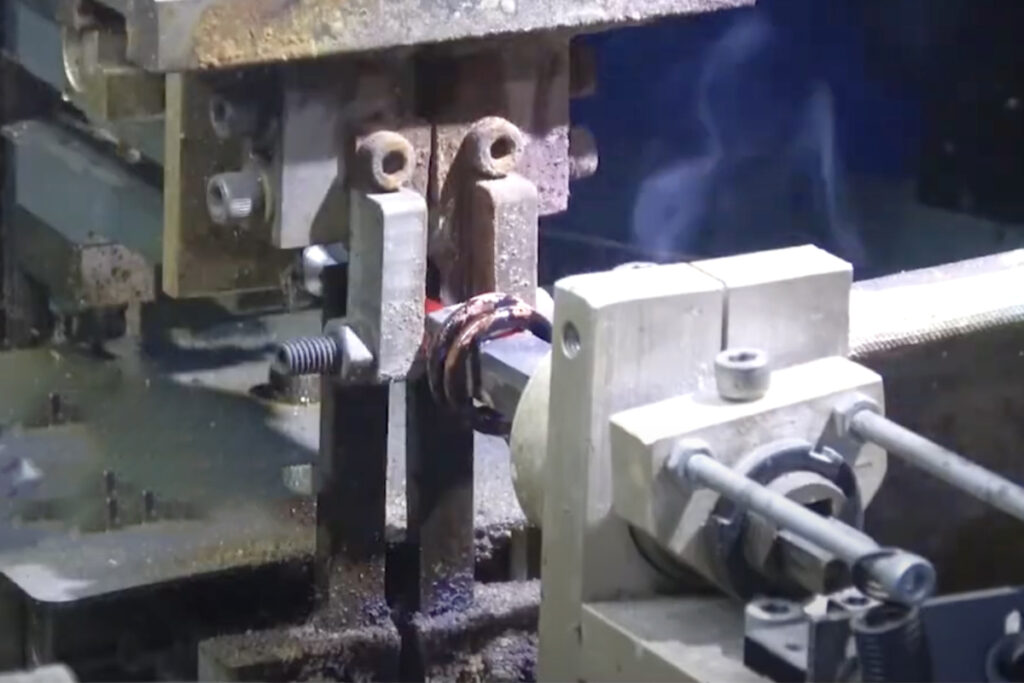
Shaping and Finishing: The Final Frontier?
Once sintered, the burrs need shaping and finishing. These burrs are then meticulously shaped, sharpened, and polished to achieve the desired geometry and surface finish. At ShenTools, we have a team of experts (I like to call them the “Burr Whisperers”) who ensure each burr is crafted to perfection.
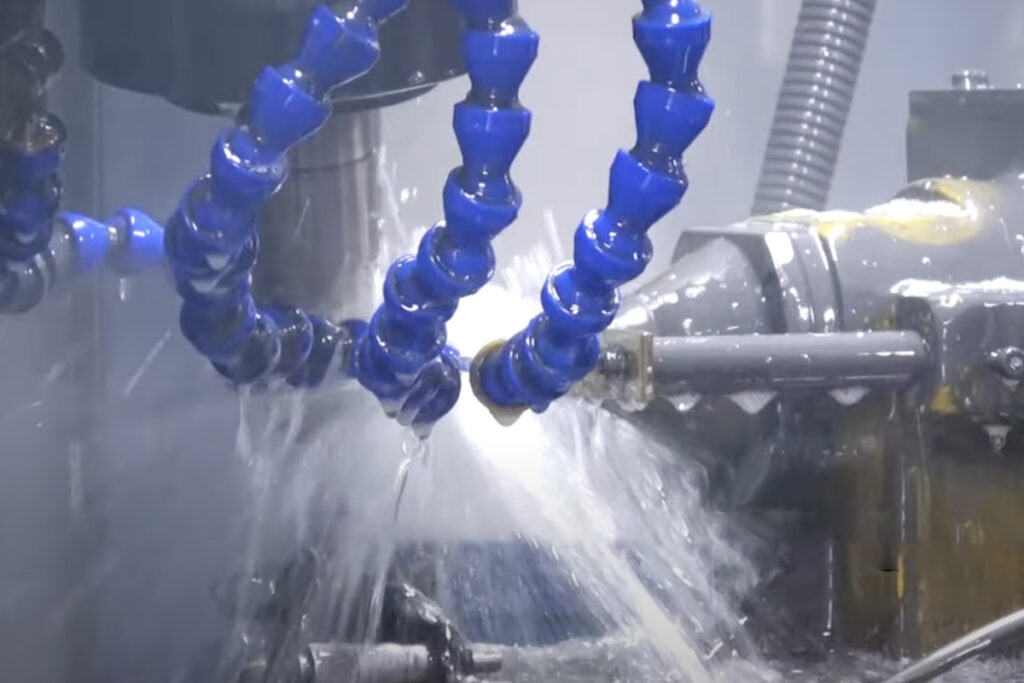
Why All This Fuss?
Quality, my friend! At ShenTools, we’re obsessed with it. We know that counterfeit products are a bane, and it’s why we’re committed to a process that guarantees top-notch quality. Every step, from tungsten extraction to the final polish, is crucial in ensuring our burrs’ performance and longevity. And it’s not just about the product; it’s about trust. It’s about knowing that when you pick a ShenTools burr, you’re choosing excellence.
Conclusion
To sum it up, making tungsten carbide burrs isn’t just a process; it’s an art. An art we at ShenTools have mastered over the years. Our commitment to quality, precision, and innovation ensures that every burr you get from us is a masterpiece in its own right. So, the next time you hold one of our burrs, remember the journey it’s been through. And know that, just like every masterpiece, it was crafted with passion, dedication, and a sprinkle of ShenTools magic.
Choose ShenTools. Choose quality. And always, always choose to be informed.